Read any scientific journal or visit any local trade show, and it will be almost impossible not to see something about “3D Printing”. It is the hot topic when it comes to “what’s new in the world of manufacturing.” Along with the buzz, comes many perceptions on what the technology is, and what it can do. The term “3D Printing” is often associated with rapid prototyping. In other words, someone needs a part that physically represents what they want the end product to be, however, it’s not expected to perform how the final product will. These prototypes are typically produced with entry-level machines, using materials and processes never meant for production.
This is in contrast to the production-based machines, materials, and process specifications. The result is production-rated hardware used all over the aerospace industry. Enter the new classification of “Additive Manufacturing”. Under this realm, companies produce parts that meet standard aerospace tolerances, and in many cases, meet the same mechanical properties inherent in parts produced using traditional manufacturing methods such as injection molding or machining.
To give an example, it’s akin to the difference between a hobbyist mechanic turning an aluminum rod on the lathe he purchased at the local discount store, versus a professional machine shop turning the main rotor shaft for a helicopter. The actions and principles behind each situation above are the same; it’s the controls and equipment behind the actions that differ. At the end of the day, it doesn’t matter whether you call it 3D Printing or Additive Manufacturing. The key is to understand the vast variety of processes and materials available, and applying the correct one of each to your application.
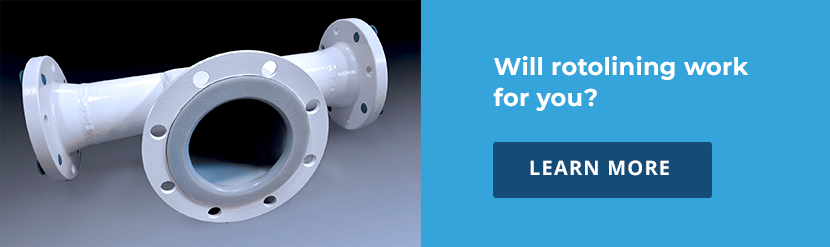