How to Minimize Contamination in Semiconductor Manufacturing
Each semiconductor fab institutes stringent policies to eliminate potential contamination and maintain the highest purity standards. These standards apply to every stage of the manufacturing process, particularly for the variety of fluids used for cleaning, etching, planarization, and other stages of the production cycle.
The rotomolding process serves as the best technology to manufacture containers that will maintain purity and eliminate potential sources of contamination. This combination of process (rotomolding), product (high-performance polymers), and RMB quality procedures will supply components with a long service life and help overcome the challenges faced by semiconductor fabs and component suppliers.
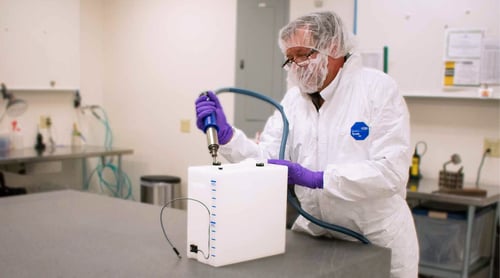
The process of rotational molding
Rotational molding leverages the superior characteristics of high-performance resins, with the fabrication technology offering unique advantages over blow molding or injection molding. One major advantage is that rotomolding creates containers, such as vessels, tanks, or bottles without an interior seam, allowing for a free flow of liquids. The seamless, smooth interior surface also eliminates the possibility of sediments or contaminants accumulating along the interior seam, which is common to blow molding and injection molded parts.
Additionally, the polymers supply a durable container that can withstand harsh environments and handling without chipping, shredding, cracking, or breaking — a potential problem with quartz containers.
The same process used for rotolining larger vessels is the one used for rotomolding. RMB selects the appropriate polymer resin, melts it, and rotates the mold biaxially to create the container. This processing method can also be used to create recessed fittings or different geometries with curvature or contours. These variations can help accommodate customer requirements for cabling, mounting devices, and other features on the containers. Or they can be used for level sensors or other peripherals.
Original equipment manufacturers constructing wet benches and other processing stations for semiconductor manufacturing often specify a desired resin, most often either polyvinylidene fluoride (PVDF), perfluoroalkoxy (PFA), or high-density polyethylene (HDPE). RMB can also provide high-purity fittings for the tanks that are compatible with the containers.
Rotomolded containers using these and other high-performance polymers allow semiconductor fabs to:
- Retain every drop of liquid
- Protect against sedimentary or bacterial buildup
- Avoid leaks or container failure
- Extend the useful lifespan of the container
- Expedite project completion timelines due to simpler mold creation compared to other technologies
High-performance polymers
High-performance polymers are well-suited to withstand harsh conditions common to semiconductor manufacturing, yet offer a more cost-competitive option compared to alternatives for fluid containers. In addition to helping fabs achieve desired purity requirements, highly stable polymers supply fabs with the functionality, performance, and durability that help manufacturers overcome challenges and achieve production goals.
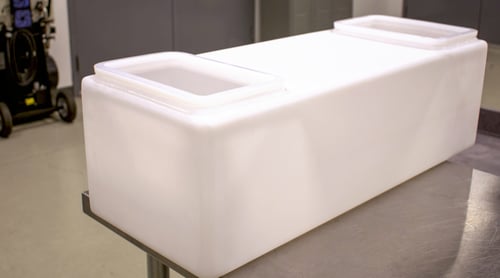
While there exists a vast universe of polymer types, a small handful comprise the types most commonly selected for high-purity applications in the semiconductor industry. Among high-purity polymer resins, PFA is the material most often requested for semiconductor applications due to its chemical compatibilities and thermal processing limits.
PFA has an extremely high processing temperature. It is stable and can be used in applications that experience temperatures greater than 400° F while maintaining its chemical compatibility. It is well known for its resistance to acids and bases.
Customers will often specify their preferred polymer resin for rotolining. When unsure, the engineering staff at RMB is available for consultation. Here are some engineering properties to keep in mind when specifying the polymer for a semiconductor or high-purity application:
- Specific heat of the material. This is the amount of energy per unit volume required to raise the temperature of a material one degree. RMB can help specify the heat energy for any given polymer and advise which material and size tank will work best in the process when there are high thermal requirements.
- Material strength. Look for materials that have high strength characteristics, or a large area of application potential according to the stress-strain curve. While a polymer’s ultimate tensile strength may be higher or lower than alternative materials, these alternatives can fail abruptly. Failure, such as a glass container breaking into shards, can instantly ruin whatever batch or single wafer is in production in that vessel.
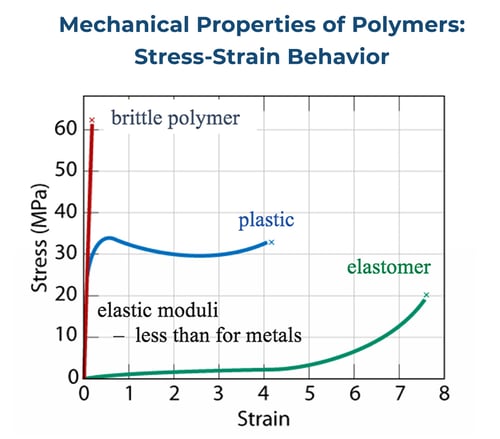
Note that the area under the stress-strain curve displays the amount of energy required to create failures in the material. Polymers that are rotationally molded offer high strength characteristics, or a large area of application according to the curve.
- Ductility. Rotomolded polymers are very ductile. Once rotomolded into a bottle, tank, or vessel, they will not fail or become brittle. Upon impact, the polymers will not break or chip like glass would, thus contaminating the contents of the process. In contrast, glass has no stretching or percent elongation. Many of the polymers utilized by RMB for rotational molding can stretch from three to nine times their original length before reaching a fracture point.
- Surface energy. Thermoplastic polymers have varying degrees of surface energy, which characterizes their bonding capabilities. High surface energy allows easy bonding, whereas low surface energy does not. The lower the surface energy, the greater the resistance to bonding, equaling a greater capacity to repel liquids as diverse as oil and water, among other substances. The surface energy of PFA, for example, prevents anything from sticking to it. It aids fluid recuperation as well as the ease of flushing foreign or unwanted objects from its surface to prevent contamination.
This quality, combined with a seamless tank interior from rotomolding, helps promote the high-purity atmosphere required for semiconductor manufacturing — regardless of the phase or processing step.
Superior quality controls for purity
High-performance polymers provide a material source that helps solve some of the most common industry pain points in semiconductor manufacturing. These pain points are related to fluid containment, such as leaching, contamination, durability, and lifespan. When rotomolding is applied to these high-performance polymer resins, it creates a container particularly suited to the requirements in the semiconductor industry.
RMB takes every possible step to ensure its final product will provide the cleanliness and purity required in the semiconductor industry. For example:
- Virgin, certified resins. RMB restricts its material usage for rotomolding processes to virgin, certified resins. It works with all the multinational providers, sourcing materials from DuPont, Chemours, Daikin, or AGC, Inc. The materials contain no other monomers or polymers, with the sole material component restricted to the polymer requested by the end user.
- Purity and traceability. RMB maintains lot traceability and follows it through the rotomolding process to guarantee the material remains pure. When installed in the customer’s system, at whatever stage of the semiconductor manufacturing process, the material will be as pure as when RMB first purchased it.
- No regrinding or recycling. RMB does not recycle or regrind its polymers. Any excess material or drop from the manufacturing processes is sent to a secondary firm for reuse at a different facility. While the material is not wasted, it’s also not used for high-purity rotomolded products.
- Strong shapes. RMB creates cylindrical or spherical tank shapes, which are easier to mold than to fabricate. The radius of a cylinder or sphere is inherently stronger than a container with a squared-off, 90-degree angle at the bottom. A rotationally molded sphere or cylinder helps increase the container’s strength.
- Dedicated clean room. The final cleaning and bagging occur in the dedicated clean room at RMB. This is standard operating procedure for any high-purity product manufactured by the company. In the clean room, every product surface is wiped with isopropyl alcohol, and all products are placed in certified bags. The bags are tied off prior to moving them through the airlock to shipping.
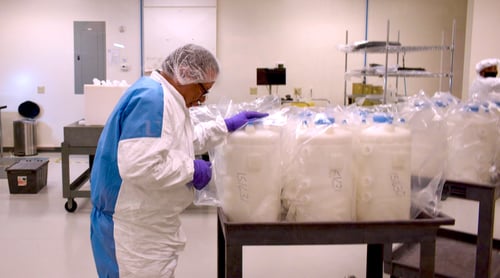
The three components of container manufacturing for the semiconductor industry — the process, the product, and the quality control procedures — ensure that seamless containers eliminate potential contamination points. Rotomolding creates containers eminently suited for high-purity applications. Contact RMB today to learn more about high-purity bottles, tanks, or vessels.