Innovative Approach to Aerospace Components: Flexibility of Polymers and Processes vs. Traditional Subtractive Metal Processing
What can 3D printing do that traditional manufacturing cannot? It can do a lot for aerospace components that was not formerly possible. Among the new materials and processes revolutionizing traditional manufacturing, the combination of high-performance polymers and 3D printing technologies stands as a disruptive innovation has opened new realms of possibilities for parts design in industries of all types, including aerospace.
Additive manufacturing has not and cannot replace traditional technologies entirely. A finished aircraft incorporates multiple materials and processes, including traditional subtractive manufacturing, rotational molding, injection molding, metallic weldments, and composites.
However, additive manufacturing is a smart choice for components such as shrouds, trays, bracketry, and environmental control system (ECS) ducting. The parts need to be lightweight and able to withstand variable temperatures, some impact, and potential chemical exposure.
Overall, 3D printing expands the options for aerospace engineers to design and produce geometries that would be extremely difficult or impossible using these other technologies, such as metal weldments or composite layups. The two processes both produce useful parts for aircraft and other vehicles; however, they use methods that are direct opposites.
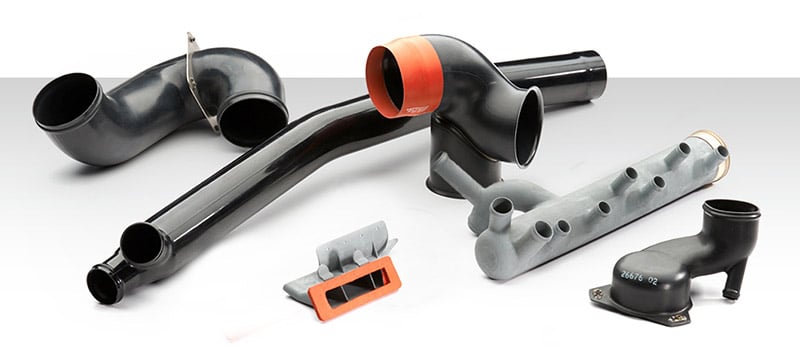
Opposite ends of the spectrum
Additive manufacturing is so called because it builds the component from a computer-aided design (CAD) file, adding one layer at a time, with a polymer resin selected for the properties it can lend to the finished piece.
In contrast, subtractive manufacturing starts with a solid piece of material in a block, bar, or rod, which is made of metal or plastic and relies on computer numerical control (CNC) machining to remove material a layer at a time to reveal the desired shape. This can involve cutting, drilling, grinding, or hollowing out the solid object, as opposed to adding to the shape layer by layer.
Part sizes made by additive manufacturing are limited by the size of the printer. Therefore, other processes are better suited to make large parts. Small parts or consistent runs with a short lead time are a great match for additive manufacturing.
Subtractive manufacturing can require a long setup time, programming, and tooling, which adds to the initial expense per project run. This makes it better suited for high-volume production, to amortize the set-up costs on a per-unit basis.
And, as aerospace companies commit to sustainability goals, companies should note that additive manufacturing can decrease the scrap waste associated with subtractive manufacturing. RMB recycles the materials that it sinters, which is compliant with the customer’s specifications.
High-performance polymers make a difference
3D printing can use a variety of materials, from polymers to ceramics and metals. Ductwork and other components for aerospace often rely on certain classes of polymers that exhibit the characteristics desired for the environments encountered in aerospace applications. These often include polyetheretherketone (PEEK), polyetherketoneketone (PEKK), polyetherimide, polyamide 11 (nylon 11), or polyetherimide (Ultem®). RMB’s expertise is currently with polyamide 11 and 12 formulations.
Each has various characteristics that offer functionality or processing capabilities, such as the ability to withstand temperature extremes, offer flame retardance, or provide chemical resistance. Any of these conditions may be encountered in an aerospace application.
Benefits of additive manufacturing for aerospace components
Now to examine the advantages that additive manufacturing technology offers for aerospace components and parts:
- Customization and design iteration. Additive manufacturing allows for the rapid production of customized ductwork tailored to specific projects. It empowers designers and engineers to iterate designs quickly and efficiently, resulting in reduced lead times and cost savings during the critical design review and early production phase.
- Increased flexibility. Working from CAD files allows last-minute revisions if the engineers or designers need to change the design prior to printing the part.
- Greater speed and increased cost efficiency. This style of manufacturing works from a CAD design supplied by the customer, which eliminates the need for molds or long setup times. This speeds the process from order to delivery in one-third of the time required by traditional, subtractive manufacturing or methods that use molds. It also cuts costs by eliminating the molds or fixtures commonly required with other types of manufacturing.
- Broad material selection. Additive manufacturing relies on advanced polymers across a wide range of functional properties to meet project specifications.
- Ductility. A common pain point for customers is related to parts breaking during installation on the aircraft. This occurs most often with thin wall composite/fiberglass ductwork. A damaged ECS duct being installed on the aircraft causes critical cost and delivery delays that may impact the delivery of the aircraft. A professionally printed polymer product can help to eliminate breakage during installation.
The corrosion resistance property alone makes polymers an ideal material selection for ductwork installations in harsh environments, where exposure to moisture, chemicals, or high humidity can often compromise the durability of traditional metal ducts.
This allows production of lightweight, durable ductwork that can withstand specific environmental, temperature, and pressure requirements.
- More complex features. 3D printing technology enables the incorporation of internal features, such as airflow optimization channels, directly into the ductwork design. Incorporating intricate internal features without seams or welding not only lightens the weight and improves structural integrity but also enables complexities beyond the capabilities available using traditional metal subtractive methods of manufacturing.
This increased intricacy and complexity comes without sacrificing structural integrity, yielding durable parts that meet performance standards.
- Less complex certifications. The additive manufacturing process slashes the number of required certifications compared to traditional manufacturing methods. For example, consider manufacturing an ECS dust using metallic weldment methods. A metal duct would require certifications for the welder, welding fill material and welding gas, material alloy, dye penetrant inspection, chromate conversion or anodize processes, and primer and topcoat paint, as required. The additive manufacturing process for the same part requires a polymer certification and one for paint, if the part is painted. As you can see, certifications are simplified for single-piece construction.
The answer to that question is yes
How durable and adaptable is the part? That is one of the most frequent questions related to additive manufacturing. As is typical in the aerospace industry, single parts or components often need value-added services or steps to make them install ready. Product enhancements for ECS ductwork often include mounting brackets, flexible silicone cuffs, or insulation.
Some features are not printable such as nutplates and rivets. Parts constructed using additive manufacturing offer the capability to add these features without compromising the integrity of the part or component.
Quality processes earn a spot as a delegated source
The stringent safety concerns and standards in the aerospace manufacturing industry cause companies to scrutinize and verify the quality processes of every vendor. After conducting this audit, that vendor becomes a designated source for the parts they produce.
RMB Products has instituted robust quality processes to earn a position as a “dock-to-stock" supplier for its customers, for parts that ship directly into their inventory. This designation benefits both parties but particularly the customer. It means that at the customer’s manufacturing plant, once the aircraft moves into position during its assembly, the part can be pulled from stock and immediately installed onto the aircraft.
This capability to produce parts ready to install upon delivery saves the customer the time, expense, and paperwork involved with sending parts to third-party suppliers for value-added finishing services, such as nuts, plates, rivets, or insulation. It reduces the risk of error and shortens the project timelines by condensing the manufacturing process for these components.
Depth of experience in additive manufacturing
RMB incorporated additive manufacturing capabilities into its service portfolio shortly after the technology was introduced almost 20 years ago. In its infancy, many product designs remained similar to those constructed using traditional technologies, or subtractive manufacturing. Over the past 5-10 years, engineers have issued designs that now take full advantage of 3D printing capabilities to:
- Reduce part count
- Reduce waste
- Improve product design and performance
- Simplify certifications
- Reduce weight
- Create complex internal features
- Integrate bracketry
- Design innovative mounting points
Overall, a comparison of additive manufacturing to traditional manufacturing highlights its potential to create more nimble, complex part designs. It supplies unprecedented design freedom for aerospace engineers while also reducing waste, leveraging the material properties of high-performance polymers, trimming weight, and eliminating the need for labor-intensive secondary tasks.
The result is a lightweight, durable, and customizable solution. While traditional manufacturing has long been the norm, its limitations make additive manufacturing an attractive alternative for some of the more complex and intricate components required in an aircraft. As the technology continues to advance, additive manufacturing will play a pivotal role helping reshape the aerospace industry while driving more sustainable business practices.
Characteristics | Additive Manufacturing with Polymer Resin | Subtractive Manufacturing with Metal |
---|---|---|
Lightweight | X | |
Short production timeline | X | |
Tooling and setup costs required | X | |
Flexibility for design changes | X | |
Welded parts | X | |
Complex features enabled | X |
Contact RMB to learn more about additive manufacturing solutions for aerospace parts. Or request a quote for your next aerospace project.
About the Author: Chris Glock
Chris Glock is vice president of program management at RMB Products. He began his career with RMB in 1991 and has held a variety of manufacturing and commercial roles within the company. His current responsibilities are program and project management. Glock has deep expertise in engineering product applications, quality requirements, and program management.