Lighter, Better, Faster — 3D Printing Technology Improves Aerospace Components
Ever since the first helium balloon ascended in Paris in 1783, inventors and engineers have sought ways to make airborne vehicles lighter, faster, and better. While modern aircraft do not rely on helium to reach the heavens, airplanes, helicopters, and rockets must attain the status of being “lighter than air” to remain aloft. Not an easy feat considering the weight of a loaded aircraft. A Boeing 747 freighter, for example, has a maximum takeoff weight is 910,000 pounds.
Removing weight from aerospace solutions and therefore the aircraft itself not only helps with fuel economies but also can extend the flight range. For example, Qantas set a flight record in 2019 with a 20-hour, nonstop trip from New York to Sydney without refueling, a feat that would not have been possible earlier in aviation history. For any ultra-long flight, weight reduction is paramount. One method of addressing this challenge is the use of thermoplastic components in place of metallic or composite parts.
Additive manufacturing, also known as 3D printing, relies on high-performance thermoplastic resins. These plastics can weigh as little as half of the metal they are designed to replace. Aircraft engineers and manufacturers can turn to plastics to reduce component weight while satisfying all the stringent engineering requirements.
According to information collected annually by the Massachusetts Institute of Technology Global Airline Industry Program Airline Data Project, fuel costs represent almost one-fourth of total expenses for domestic airlines. Every ounce saved on any component, without sacrificing critical performance characteristics, saves fuel and money.
Defining additive manufacturing
Additive manufacturing is a process that allows for the creation of three-dimensional objects by adding layer upon layer of material until the desired shape is achieved. The advent of high-performance thermoplastic polymer resins expanded the capabilities of 3D printing.
These resins are engineered to lend specific properties to the finished part. These can include properties like high strength and durability and resistance to heat, chemicals, and UV radiation.
Plastics can be used in various applications, such as aerospace, automotive, medical, and consumer goods. The use of high-performance thermoplastic polymer resins in 3D printing has revolutionized the manufacturing industry, making it possible to create custom parts with complex geometries and with incredible precision and speed.
The process involves no molds or special tooling. The part can print from a customer-provided CAD model. This can significantly accelerate the first article’s time frame from months to weeks.
Cutting out complexity from complex components
Additive manufacturing, printing from a computer-aided design (CAD) file, allows printing of complex parts while reducing the lead time, paperwork, and complexity involved in traditional manufacturing processes.
Part count reduction. The process enables printing of parts with complex geometries in a single piece, to reduce overall part count. Traditional manufacturing for a duct, for example, might involve welding, molds, rivets, brackets, cuffs, bonding, and more. In the case of 3D printing, all design features can be incorporated and printed in a single process for a single part.
Inventory reduction. The single-piece process reduces inventory requirements for all the separate components, saving space and paperwork.
Fewer certifications. Each piece in traditional manufacturing requires the manufacturer to maintain certification traceability for each item; this is needed for every rivet, washer, special process, adhesive, paint, alloy, etc.
Shelf-life concerns. In the case of paint and adhesives, inventory management includes shelf life. The shelf life for typical adhesives can be as little as six weeks and often not more than one year. Additive manufactured parts, with the reduced part count may not completely eliminate shelf-life management issues, but it will certainly reduce it.
Expediting delivery. Every part that is eliminated by a single-piece process eliminates potential supply chain impacts to an on-time delivery, bringing final product completion within the right time frame and within budget.
Adding complexity back in where it's needed
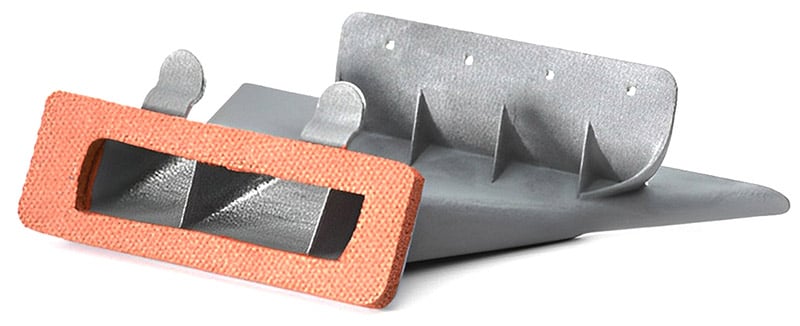
A process like laser sintering allows engineers to incorporate internal features into a complex design to solve issues that traditional manufacturing cannot address. For example, an air duct might be experiencing an excess pressure drop. Additive manufacturing can print a flow directional feature inside of the duct as an integral design element on a single component. This can help normalize airflow through the duct, increasing airflow efficiency.
Other processes, including those that incorporate thermoplastic resins (e.g., injection molding), could not include that type of feature without adding extra parts. The design might involve riveting and bonding. A composite part might need a reinforcement layup to accomplish the same design element.
Each extra part adds weight, time, and certifications. These factors multiply the potential impact on quality or delivery time. Using additive manufacturing to build it as a single part simplifies the design, reduces the impact, expedites delivery, and reinforces quality.
Engineering design support
RMB Products entered the 3D printing market, specifically laser sintering, in 2005. Selective laser sintering (SLS) offers customers sophisticated additive manufacturing technology. It uses a high-powered laser to fuse small particles of thermoplastic powders together, layer by layer, to create a solid 3D object.
Compared to other 3D printing technologies, it offers the advantage of being well known for creating parts with strength and durability for a relatively low cost. This makes sintered parts ideal for use in aerospace and other industries where those polymer performance characteristics are well suited.
Laser sintering allows parts with complex geometries to be created using a wide range of thermoplastic materials. In addition, it does not require support structures to stabilize the part during the printing process, thus eliminating the time required to remove the support structures and finish the part surface.
Routine testing confirms proper polymer selection
RMB offers a selection of proprietary thermoplastic resin options. However, most often, the customer has specified a specific resin for the process. One distinction is between fire-retardant or non-fire-retardant materials. Most commercial aircraft require fire-retardant polymers, while most defense programs (but not all) use non-fire-retardant materials.
For 3D printing, RMB offers an agricultural-based, sustainable polymer option, nylon 11, which is made from castor beans. It enables aircraft manufacturers to meet parts specifications while also maintaining net-zero sustainability goals.
One hundred percent of the builds manufactured by RMB include a series of tensile bars strategically placed throughout the build. The tensile bars validate whether the sintered part will meet the requirements of the customer’s specifications. The strategic placement of the bars in the build covers the full height, to ensure no part has a defect that would impact the final product’s performance. The tensile bars measure tensile yield and ultimate tensile strength as a pounds per square inch (PSI) value as well as the percent elongation.
Elongation of the tensile bar
The elongation of a tensile bar for a thermoplastic material refers to the amount of stretching the material undergoes before it yields and ultimately breaks under stress. This property is important in aerospace applications because it can help predict how the material will behave under load.
For aerospace laser sintering applications, tensile bar testing with conforming results in the absolute best indication of a statistically controlled process. This supplies customers with the assurance of quality and reliability for any product we manufacture at the RMB facility.
Calling on 3D printing technology experience
RMB can offer engineering design support and recommendations when a project is under development.
RMB 3D printing engineers offer a depth of knowledge on each process available for parts production using polymers, whether rotational molding, rotational lining, or additive manufacturing. We can work with your staff collaboratively throughout the process and help identify areas for improvement prior to progressing to the final production stage. Request a quote for your next aerospace component project to make it lighter, better, and faster than ever before.
About the Author: Chris Glock
Chris Glock is vice president of program management at RMB Products. He began his career with RMB in 1991 and has held a variety of manufacturing and commercial roles within the company. His current responsibilities are program and project management. Glock has deep expertise in engineering product applications, quality requirements, and program management.