RMB Opens Lining Capacity for Larger Parts and Vessels
Executive summary
The U.S. manufacturing sector is poised for recovery in 2024, with certain sectors anticipating generous growth, particularly those associated with agriculture or sustainable energy sources. Discover how RMB Products has opened capacity to meet increased demand for larger, rotationally lined (rotolined) containers.
Main points:
- U.S. manufacturing sector outlook for 2024 is bright and roaring ahead for some market segments.
- RMB has new capabilities to handle larger vessels, tanks, and pipes for rotational lining.
- Learn about the superior benefits of rotational lining compared to alternatives.
While various sources post lukewarm to cautious predictions for the U.S. manufacturing sector in 2024, some segments look forward to production surges that will return business to pre-pandemic levels and beyond. For example, the chemical processing industry never waned during the pandemic era and is projected to continue at a pace of 3%-4% annual production increases.
What the pandemic era did impact was capital improvement projects as supply chain issues stalled expansion plans. Companies in multiple sectors now intend to move forward with these previously stalled objectives. Additionally, other sectors associated with sustainable energy and computer chips, for example, continue their upward trajectory and are pressed to keep up with demand.
The anticipated capital expansion projects and double-digit growth in other sectors have operators seeking larger rotolined vessels and tanks to handle production demands. RMB Products has proactively responded to this shifting landscape by expanding its capabilities to accommodate the rotational lining of larger vessels, tanks, and pipes.
A few industries worth noting that are in line for larger rotolined containers and pipes include:
- Fertilizer production. The fertilizer industry is witnessing increasing demand to feed a burgeoning global population projected to reach 9.7 billion by 2050. Companies are investing in larger lined tanks to hold larger quantities of reactive materials.
- Lithium processing. As the demand for lithium-ion batteries surges to power the shift away from fossil fuels, the need for sizable vessels for lithium processing and storage purposes has also increased. As one example of market potential, in 2022, there were 40 lithium mining projects around the globe, with more than 100 projects expected to be in operation after 2025.
- Hydrogen production. As the focus on sustainable energy solutions grows, so does the demand for hydrogen production. The planned output for green and blue hydrogen through 2030 is quadruple that of production in 2020. Rotational lining supplies protection during the hydrogen electrolyzing process, for example.
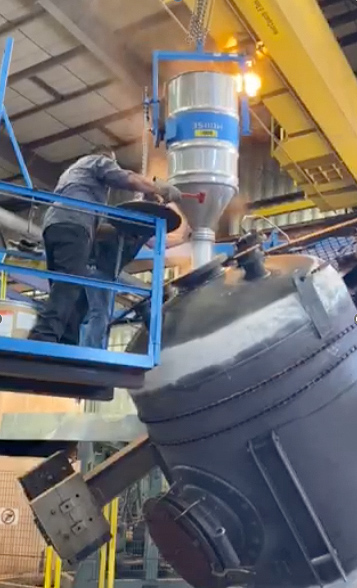
Enhanced capabilities: Bigger, better, and more efficient
RMB recently enhanced its rotational lining capabilities related to the size and weight capacity that it can accommodate in the ovens used for the rotolining process. One oven that previously was limited to a weight of 5,000 pounds is now cleared to allow rotational lining of tanks, vessels, and pipes that weigh up to 7,000 pounds, with a size capacity for parts of up to 9 feet in diameter and a height of 10 feet.
Another oven, called the Rock-N-Roll machine, can line containers, tanks, pipes, and vessels up to 20 feet in length and 6 feet in diameter with a weight limit of 5,000 pounds.
The rotational lining process
Rotational lining plays a vital role in protecting industrial equipment from damage related to corrosive and abrasive contents. This protection supplies vessels, tanks, and pipes with the integrity and longevity required for durable and reliable service, offering unparalleled benefits that set it apart from other alternative methods.
Rotational lining installs a monolithic, seamless polymeric liner inside the container or vessel. Staff selects the resin according to customer specifications and/or the anticipated or known conditions the container, vessel, or pipe will encounter during use.
Once the pipe or vessel interior is properly prepared, the resin powder is placed inside the pipe or tank and slowly rotated inside the heated oven. As the part rotates, the heat melts the resin, allowing it to spread evenly and coat the interior surface of the vessel.
The resulting liner is robust, with thicknesses reaching up to 1/4 inch — which is significantly thicker than sheet liners or spray-on coatings. The absence of hand welds or seams eliminates potential weak areas that could be attacked by corrosive chemicals. Moreover, rotational lining offers a quick turnaround time compared to other corrosion protection methods, making it an efficient choice for industries or companies with a tight schedule.
The superiority of rotational lining
Rotational lining offers unique advantages compared to alternatives, due to its unique application method and subsequent features this creates. These include:
- Corrosion protection. Industries that rely on corrosive chemicals and ingredients, such as fertilizer production, rely on rotational lining to provide a robust and seamless protective barrier to shield the vessel’s interior. This protection extends the lifespan of the vessel.
- Chemical compatibility. Rotational lining allows the selection of specific resins that are compatible with the chemicals used in processing and production cycles. The flexibility of resin choice creates a vessel or pipe able to withstand aggressive chemical exposure without degrading.
- Abrasion resistance. In addition to corrosion, certain industries handle abrasive materials as well. Certain polymers, such as high-density polyethylene (HDPE) and ethylene-tetrafluoroethylene (ETFE)/Tefzel®, offer exceptional abrasion resistance to create a more durable lining and extend the vessel’s lifespan.
- Longevity. Rotational lining typically provides a service life of 20 years or more, depending on the service environment. This extended lifespan helps stretch out expenditures for capital equipment and vessel replacement for a long-term, positive return on investment.
- Efficiency. Rotational lining offers quick turnaround times compared to other alternative corrosion protection methods. This efficiency can prove critical in industries where production schedules are tight and downtime is costly.
- Environmental considerations. A secure, reliable lining can help prevent leaks or spills of aggressive, caustic, and potentially harmful chemical substances, protecting workers and the environment. The seamless liner created by the rotational molding process eliminates potential weak points where corrosion or leaks might occur.
Available material choices for larger rotolined vessels
Furthermore, rotolining can accommodate various plastic resins, including:
- HDPE
- ETFE
- Perfluoroalkoxy (PFA) (for aggressive, high-temperature service environments)
- Kynar
- Polyvinylidene fluoride (PVDF)
This versatility allows engineers to select the most suitable resin to match their specific chemical and environmental requirements. The chemical engineers designing the equipment can select the proper resin to match the chemistries or abrasion from sand or other fine media that could erode the corrosion barrier.
Projected lifespan and cost efficiency
One of the most common questions asked about rotational lining involves the lifespan of the lining compared to alternative methods. As stated, rotational lining provides a service life of 20 years or more, depending on the service environment.
In many cases, rotational lining outperforms other corrosion protection methods. For example, rotolining has been shown to last three to five times longer than spray coatings or fusion-bonded epoxy.
Rubber linings, another common alternative, can compromise the structural integrity of equipment once they begin to fail. In contrast, rotational lining maintains its effectiveness throughout its service life.
Special considerations for ASME vessels
Handling large vessels is not without its challenges. Large tanks may have small nozzles or unique geometries that require special attention during the lining process to ensure a consistent, uniform thickness. Our experienced engineers and technicians are well-equipped to address these challenges.
Larger vessel lining projects generally involve ASME Code Section VIII parts. ASME Code Section VIII serves as a comprehensive framework governing the design, manufacturing, inspection, and testing processes for pressure vessels. It encompasses essential stipulations, specific restrictions, and optional advisory provisions related to materials, certification, and pressure relief.
The engineering team must have time to properly calculate the design, conduct a redline process with the customer for all the nozzles, accessories, and source inspections. Customers should plan ahead for any vessel but especially larger vessel rotolining projects.
Under normal operating conditions and with ASME standards to follow, these projects can take from 10 to 12 weeks to complete. However, always ask for a quotation when facing an emergency. When line space is available, RMB has expedited projects down to a five- to six-week turnaround, without compromising on quality.
While the chemical processing, oil and gas, and mining industries have traditionally relied on rotational lining to protect capital equipment, the capability to line larger pipes and vessels opens new possibilities for these industries as well as other growing market sectors that deal with aggressive chemicals.
RMB’s adaptability to a range of other industries and unmatched durability, quality, and expertise make rotational lining a practical and sensible option for corrosion protection.
Contact us to explore how we can meet your application needs, whether for larger vessels or more standard projects. Or request a quote to get started on your corrosion protection project.