Rotolining is used to install fully bonded, seamless liners in piping or process equipment. It is corrosion and abrasion resistant for chemical services. The process works by rotating the part in an oven, allowing gravity to evenly distribute a layer of molten polymer on all internal surfaces. The result is a seamless lining that conforms to complex shapes and is virtually free of any stresses.
- Seamless liner reduces failure points
- Exceptional corrosion resistance of acids
- A fully-bonded liner reduces the risk of delamination
- High operating temperatures (up to 500° for PFA (Teflon))
- Mechanical bonding eliminates adhesives
- Longer service life (Fluoropolymer or Olefin lining)
- Compatible with ANSI flange, Victaulic, and sanitary flange fittings (and more)
- Easily line complex structures
- Strong chemical and abrasion resistance
- Line pipe spools and fittings up to 20 feet in length
- Line large-diameter vessels up to 10 feet
- Lining thickness up to 0.450″
ROTOLINING MATERIALS
HDPE (high-density polyethylene), ETFE (Tefzel), PFA (Teflon), PVDF (Kynar), Nylon 12, ECTFE (Halar)
vs Sheet Lining
- Seamless liners – Eliminates failure-prone weld joints found in sheet lining
- Internal surface access – Easily line complex parts without direct access to internal surfaces while sheet lining requires direct internal access
- Reduced chemical seepage – Durable liners can coat up to 0.450“ thick vs 0.118“ thick sheet liners
- Mechanical bond – Rotolining’s mechanical bond eliminates the need for adhesives, reducing the risk of delamination
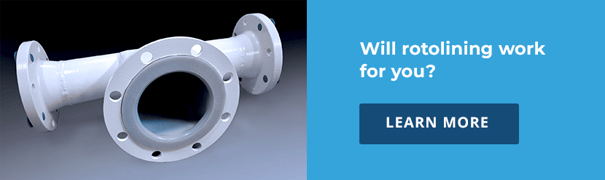
vs Powder Coating
- Corrosion resistance – Lining thickness up to 0.450″ offers greater protection against corrosion and abrasion versus powder-coating (up to 0.040″ thick)
- Crack resistance – Rotolining resists damage that thin, powder-coated liners are susceptible to. Cracks allow chemicals to attack the steel ultimately resulting in failure
- Internal surface access – Easily line complex parts without direct access to internal surfaces while powder coating requires direct internal access
vs Fiberglass Reinforced Plastic (FRP)
- Structural integrity – the integrity of the part is maintained along with the steel pressure rating; limitations of the FRP shell lowers pressure rating
- Durable – FRP is brittle and cracks when damaged causing it to fail completely
- Dual-laminate FRP includes a sheet liner offering increased protection but suffers similar problems as sheet lining
vs Fusion-bonded Epoxy Coating (FBE)
- Corrosion resistance and abrasion protection – Lining thickness up to 0.450″ offers greater protection against corrosion and abrasion versus FBE (up to 0.040″ thick)
- Internal surface access – Easily line complex parts without direct access to internal surfaces while FBE lining requires direct internal access
- Durable – FBE’s thin coating is more susceptible to damage
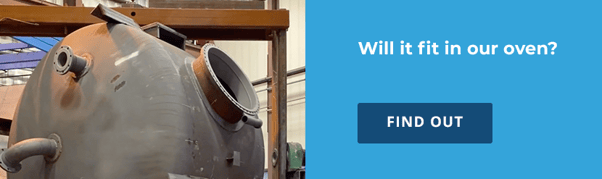
vs Glass Lining
- Superior impact resistance – Glass lining is brittle and prone to damage
- Abrasion protection – glass lining is not suitable for abrasive applications
- Easily repaired – Glass lining cannot be repaired, complete removal and re-installation is required when damaged
vs Exotic Alloys
- Lower cost – Rotolining offers a higher quality solution at a lower cost
- Faster turnaround – Parts can be completed in as little as a week versus months for exotic alloys. Rotolining lead time becomes even more favorable as part complexity increases
- Chemical resistance – Few chemicals can penetrate rotolining; exotic alloys are susceptible to corrosion depending on the chemical service used
BENEFITS AT A GLANCE
