Why Custom Rotational Molding Creates Better Aerospace Parts
Today’s commercial aircraft carry more weight in passenger luggage alone than the total weight of the original flying machine. The aircraft built by the Wright brothers weighed 605 pounds, while today’s commercial aircraft can weigh up to 485,000 pounds (220 metric tons) at its empty operating weight. Believe it or not, that weight has been trimmed down in the past several decades, thanks to aerodynamic and technological advances and the adoption of lightweight materials that replaced some metal parts.
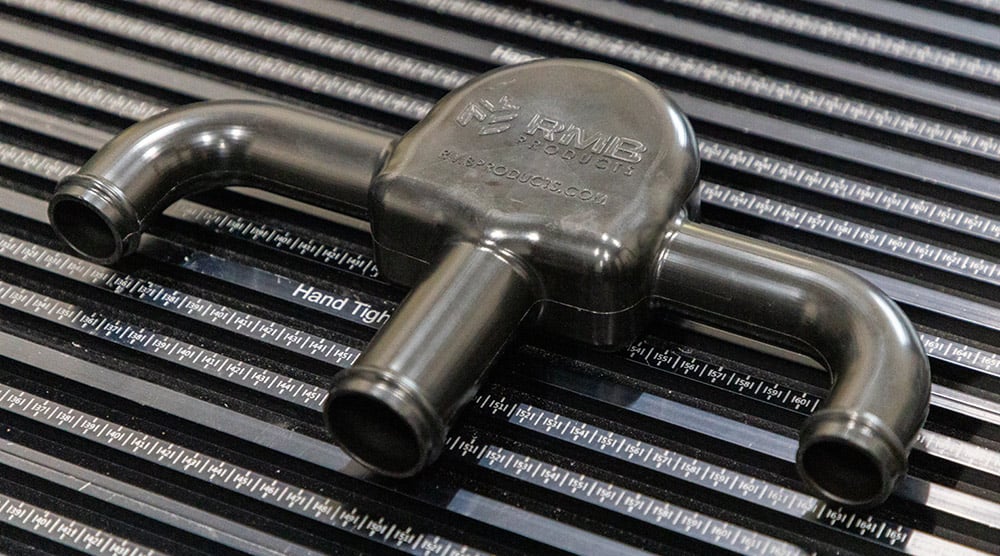
Thermoplastic resins and composites can weigh 10 times less than their metal counterparts. Both additive manufacturing and rotational molding (rotomolding) can shape or form thermoplastic resins and powders into durable components for aerospace applications. The resulting weight reduction aids fuel economies, can increase flight range, and improve corporate sustainability efforts.
RMB Products, an industry-leading, build-to-print manufacturer, has been supplying parts for major aerospace original equipment manufacturers (OEMs) and Tier I and II suppliers in the commercial and defense aerospace industry for more than 30 years. The company leverages its expertise in additive manufacturing and rotational molding to achieve the performance requirements necessary in this demanding industry.
Rotational molding uses a combination of heat and motion to melt powdered plastic resin inside a hollow mold mounted on a rotating axis. The mold rotates biaxially as it is heated in an oven. The heat melts the resin and the biaxial rotation helps the resin uniformly coat the walls of the mold.
This process creates hollow articles without welding lines. Part size is limited only by the size of the mold. RMB has decades of experience leveraging rotomolding to produce parts that help control and reduce costs while producing high-quality aerospace components. The robust and durable aerospace parts help eliminate damage and breakage common with metallic and composite details. The parts are molded with polyamide Nylon 12, which is available in both flame retardant and non-flame retardant formulations and is resistant to many chemicals.
Importance of virgin resins
RMB strictly relies on virgin resins for its rotational molding processes. Virgin resin lends consistent quality and more predictable physical properties compared to recycled resin. It supplies higher strength, improved impact resistance, and better resistance to environmental factors, such as UV rays, chemicals, and/or temperature variations, compared to recycled resin.
Types of thermoplastic and fluoropolymer resins used in rotational molding typically include Nylon 11 and 12 and polyvinylidene fluoride (PVDF). A proprietary resin like RMB 437 (Nylon 12) is a high-impact, non-halogenated, flame-retardant, polyamide-based resin that was specifically formulated for aerospace environmental control system (ECS) ducting due to its excellent physical properties, low moisture absorption, chemical resistance, and ease of processing.
Specified for the Qualified Product List
RMB takes total ownership of the polymers it creates. The resins are compounded in-house, cryogenically ground, and tested extensively to verify performance characteristics. RMB 437 is an approved fire-retardant Nylon 12 material that is used extensively in the aerospace industry.
The approval process to be certified to an aircraft OEM specification is both challenging and rigorous. These standards are necessary to ensure that the parts will supply reliable, durable performance and meet stringent requirements.
The company must meet various certifications, such as ISO 9001 for quality management systems and AS9100 for aerospace-specific quality management. The extensive documentation required for these standards requires detailed Standard Operating Procedures, work instructions, and supporting operational and quality documentation. The evaluation and certification require annual third-party audits, which assess and rate the accuracy and effectiveness of the quality management systems.
The rotational molding for aerospace process step by step
Rotational molding provides a viable manufacturing process to create complex, hollow geometries. When compared to alternate manufacturing processes like additive manufacturing (laser sintering/3D printing), the rotational molding process can produce larger parts up to 6 feet long and as much as 6 to 8 inches in diameter.
The rotomolding process at RMB typically relies on various polymers in the polyamide and fluoropolymer families and is conducive to parts 6 feet long or less. In every industry, there is not a one-size-fits-all process. Therefore, a duct larger than 6 feet in length would more than likely use a composite material. For ducts that are less than 6 feet in length consider rotational molding and for ducts or components less than 18 inches in length, consider 3D printing.
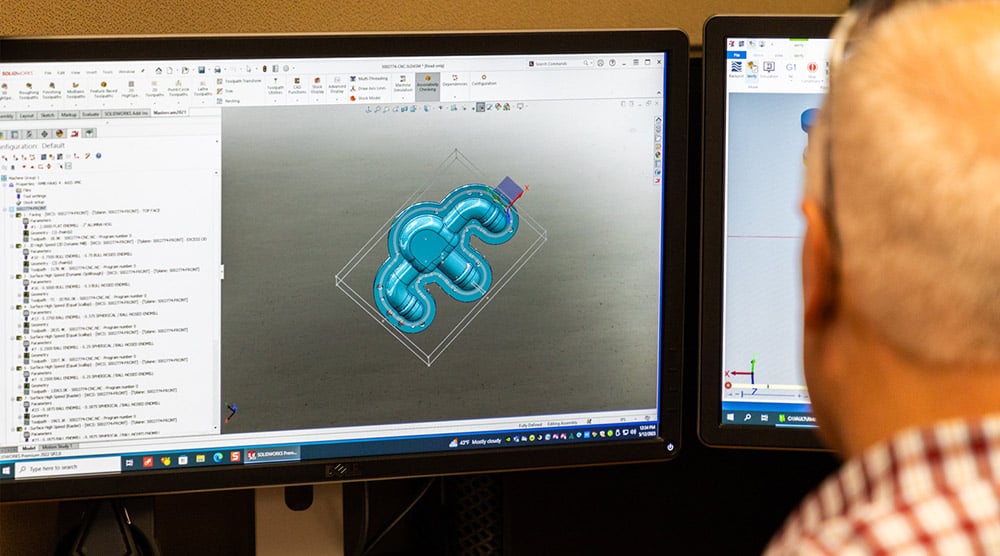
To help you gain insight into the rotomolding process, we’ll walk you through an example of manufacturing an aerospace ECS duct at RMB.
- Computer Aided Design (CAD) model and mold design: RMB starts with a CAD model of the customer’s part. A thorough review of the customer’s engineering data set includes:
- Critical dimensions for the part include factors such as:
- Size (length, width, height)
- Geometric features
- Weight
- Wall thickness
- GD & T (geometric dimensioning and tolerancing)
- Critical dimensions for the part include factors such as:
- Tool path creation: Tooling engineers at RMB create a tool path for computer-aided manufacturing (CAM) program validation, ensuring the accuracy of the tooling program.
- Machined mold assembly: The mold is Computer Numerical Control (CNC) typically machined in an aluminum alloy and assembled for use on RMB’s molding equipment.
- Molding process: The mold is mounted on the arm of a rotational molding machine. A precise amount of the specified plastic resin is poured into the mold, followed by the closure of the mold’s upper half. The mold arm is indexed into the rotomolding machine to begin the molding process. The machine rotates the arm biaxially, which evenly distributes the plastic resin throughout the mold’s interior surfaces to create a uniform wall thickness part.
- Material selection and compliance: One of RMB’s most common proprietary aerospace materials used in its rotomolding process, RMB 437 Nylon 12, meets several commercial aerospace flammability standards, including the 12- and 60-second vertical burn test requirements of FAR25.853.
- Cooling and annealing: Cooling techniques involving air, fans, and water spray are employed to crystallize the plastic and allow it to shrink away from the mold’s interior walls. If required, annealing can be performed to remove any molding stress.
- Unclamping: After the cooling process, the mold is unclamped, and the upper portion is removed to access the molded part.
- Robotic trimming: RMB utilizes robotic trimming with a multi-axis router to achieve reliable and repeatable precision. This advanced trimming process ensures the parts are trimmed to meet the customer’s specifications.
- First article inspection: RMB performs an AS9102 First Article Inspection, providing comprehensive documentation to the customer and ensuring quality control and adherence to the customer’s engineering requirements.
Rotational molding capacity for aerospace parts
RMB operates seven rotational molding centers, with several that are specifically designated for aerospace components. It also operates three CNC robotic trimming centers, with three- and four-axis capabilities to trim the rotomolded part to the customer requirements. Trim operations include drilling holes for rivets and fasteners and routing geometric features.
Suppliers to the OEM or Tier I and II manufacturers need third-party certifications and audits, not just for materials used but also to prove that quality processes, manufacturing equipment, and staff training meet certification standards. RMB has been ISO and AS audited and registered for 20 years. The staff is trained by the equipment manufacturers to ensure all equipment is maintained in a production-ready state 24/7.
Rotomolding has proven to be a highly advantageous manufacturing process for aerospace components. RMB’s meticulous attention to detail and state-of-the-art machinery ensures the production of aerospace parts that consistently meet customer specifications. And remember that RMB is certified to supply parts to any of the major aircraft OEMs or Tier I and Tier II partners. Request a quote for your next aerospace project.
- About the Author: Chris Glock
Chris Glock is vice president of program management at RMB Products. He began his career with RMB in 1991 and has held a variety of manufacturing and commercial roles within the company. His current responsibilities are program and project management. Glock has deep expertise in engineering product applications, quality requirements, and program management.