It is not uncommon for epoxy-coated fittings to fail within 1 year of service in brine pipeline applications. Average service life is likely 5 to 7 years. What if there was a way to increase service life to 20 years or longer?
With HDPE rotationally lined fittings, service life can easily exceed 20 years due to a combination of the benefits from the HDPE material and rotational lining process. HDPE is well known to protect against corrosion and abrasion from brine water. United Pipeline has been installing its HDPE Tite Liner™ system for over 30 years with great success. By lining the fittings with HDPE, the pipeline owner could expect the same service life in the fittings as they see in the straight sections.
Rotational lining also eliminated many failure modes of coatings. One such failure is poor bonding, which can be a common failure mode for coatings. With rotational lining, the liner is mechanically bonded to the metal substrate with a bond strength greater than the tensile strength of the HDPE material. This is tested with a “float roller test” per ASTM D3167.
Additionally, with rotational lining, standard lining thickness is between 0.250” and 0.320”, with a maximum achievable thickness of 0.500″. Coatings are much thinner, with coating thickness of 0.025” as a common application thickness. The thicker HDPE rotational liner is much more resistant to corrosion and the risk of abrasion from entrained solids often present in brine service. The HDPE liner will have no holidays and is tested via spark test up to 21,000 V per NACE SP-02-74.
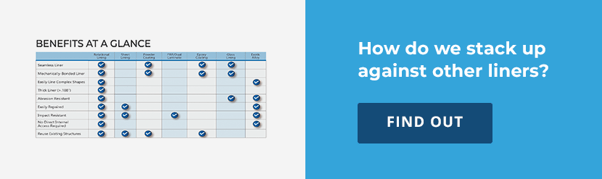
To summarize, the combination of the thick mechanically bonded HDPE rotational liner eliminates the failure modes of coated fittings. With a service life matching that of Tite Liner™ already common in lined brine pipelines, rotationally lined fittings also provide an expected life of 20 or more years. For case history, please read Texas Chemical Plant Validates Corrosion-Protection Performance of RMB Products’ Rotationally Lined Fittings