Ready Response: RMB Solutions Help Ease Emergencies
Colorful language might be the initial, gut instinct reaction to a leak or failure at the job site. The next step requires finding a solution — and fast. Across industries, companies can suffer substantial losses when an emergency occurs. Unexpected equipment failures, particularly within the chemical processing or oil and gas industries, can disrupt operations and translate into substantial downtime and a financial hemorrhage.
One of the most egregious offenders is corrosion. The Financial Times estimates the annual cost of corrosion to be more than $3 trillion, which is almost 3.5% of the global gross domestic product. On a more granular level, the staggering costs associated with unplanned downtime due to equipment failure, regardless of its cause, can equal hundreds of thousands of dollars per day. These disruptions can even impact the downstream customer, who requires their products as feedstocks to their output.
Companies need a reliable business partner with the capabilities to manage emergency requests quickly and efficiently, which is why so many customers rely on RMB Products. RMB has tailored its business model to provide a rapid response with a quality output for emergency projects related to the rotational lining of pipes, vessels, and columns.
The three major industries that most commonly require emergency services for repairs are chemical processing, water treatment, and oil and gas operations. Chemical processing plants most often report faulty equipment, damaged by the aggressive chemicals used to process and manufacture other chemicals, polymers, and specialty products.
Discovering equipment failures
There are several types of failures that producers experience involving polymer-lined and coated equipment. Common components RMB sees on an emergency basis include:
- Stripping columns previously lined with a loose liner or a sheet liner, which has permeated, collapsed, or failed at the welded seams
- Process vessels at their end of life, which are showing signs of failure on the exterior indicating that the liner or coating has been compromised
- Pipe fittings and manifolds, which have a slip liner or spray coating
- Pump casings, support rings, and reducing flanges are often needed on an emergency basis and often require fabrication by RMB
Among the assorted reasons for failure, some of the most common are:
- Chemical attack: While polymer linings and coatings provide resistance to many chemicals, if the pipe or vessel is exposed to chemicals or concentrations that are incompatible with the chosen resin, they will degrade the protective lining or coating over time.
- Improper installation: If the original coating was improperly applied, voids or thin spots can develop, leading to premature failure. Since the welding performed on sheet-lined equipment is done by hand, the weld seams are susceptible to variations in quality and reliability, which can lead to premature liner failure. Liners have been known to fail due to the smallest welding deficiencies.
- Abrasion: The continuous flow of abrasive materials can wear down the lining.
- Thermal cycling: Repeated and rapid temperature changes can stress the lining, leading to cracking or delamination.
- Changing service conditions: When conditions inside the pipe change without a corresponding review of the liner’s suitability, failures can occur. These changes may include increased pressure, temperature fluctuations, or chemical composition.
- Aging: Over time, even the best linings can degrade. Regular inspections can forestall failures to allow companies to schedule repairs during planned shutdowns. Companies need to monitor any deviations from standard operations and be proactive about equipment maintenance, particularly when there are changes in the processing environment or cleaning procedures, for example.
Preparedness makes a difference
Many of the issues that cause equipment failure can be traced back to the initial resin selection, which is why it helps to partner with a company that offers decades of experience working with high-performance polymers. RMB’s staff can recommend the most appropriate resin to match the conditions within the application when supplied with the specifications and environmental challenges known to the operations manager. RMB also maintains an extensive inventory of resins for rotolining, to avoid delays associated with a lack of available materials.
The rotolining process requires tools and hardware that are properly sized to seal the openings and rig the equipment that requires lining. RMB keeps a large inventory of closure plates, rings, hardware, clamps, and chains in working order, so that vessels, pump housings, and piping that arrive on short notice can be added to the production queue without delay.
In addition, RMB has installed advanced infrastructure designed to rapidly facilitate relining and repairs, such as a pyrolysis burnout oven installed in 2018. This high-temperature, standalone bake-off oven measures 13 feet wide by 25 feet deep and is specifically designed to remove or burn out old liners or organic materials from metal pipes and components. The high temperatures within RMB’s burnout oven effectively break down and remove old liner material, leaving the metal substrate ready for a new liner application.
Pyrolysis bake-off oven (right); industrial paint booth (left)
Staffing, a critical factor for speed
Thanks to cross-training on the equipment utilized for burnouts, material preparation, rotational lining, and trimming, RMB can leverage a flexible, versatile workforce that’s trained to address any situation, including emergency projects. In fact, at least 20% of the rotolining projects at RMB are in response to equipment failure or require an emergency response. When a rush project enters the plant, RMB pulls out all the stops, including scheduling multiple shifts, assigning overtime, or working on weekends as needed. This flexibility helps RMB reshuffle priorities to adjust for emergency situations.
The company also maintains partnerships with local transport firms to facilitate rapid and efficient transport to and from its manufacturing facilities, emphasizing RMB’s end-to-end service provision.
Making an emergency request
The process to initiate an emergency project with RMB is straightforward. Customers can contact the team directly through the website to set the process in motion. Background materials that can help expedite the process include:
- A detailed briefing
- Photos or drawings
- Current operating conditions
- Desired timeframe for repairs
While the responsibility of logistics predominantly lies with the customer, RMB offers guidance, ensuring the customer feels directed and less overwhelmed during an emergency.
Case studies demonstrate the benefits of a swift response
Gulf Coast oil and gas company pipe failure
- Background: A hurricane in the Gulf Coast caused considerable damage to an oil and gas company’s platform, including the demolition of their fiberglass-reinforced plastic piping. The storm also harmed their operational unit. The initial target was to resume operations in eight weeks.
- Solution: RMB stepped in to design, fabricate, line, paint, and ship the required replacement piping system, complete with the necessary hardware. The task was completed in six weeks, to enable the company to resume operations as planned.
Specialty chemical products supplier pump mishap
- Background: On the verge of launching a new product line, a specialty chemical products supplier faced a setback due to an accidental gouge in the liner of a new acid pump. The original equipment manufacturer estimated a four-week wait for a replacement.
- Solution: After being contacted, RMB’s service department promptly removed the damaged liner and installed a new perfluoroalkoxy (PFA) liner using its rotational lining equipment, all within three days. This swift intervention enabled the supplier to launch the new product line as scheduled.
Petrochemical company’s stripping column failure
- Background: A major plastic resin supplier experienced an unexpected failure in a lined stripping column when a leak occurred on the exterior of its carbon steel shell. The corrosion-resistant liner was compromised by the chemical stream, which caused it to collapse. This left the metal vulnerable to corrosive failure. While some processors maintain spare units for emergencies, many are restricted by budgetary concerns and are unable to do so.
- Solution: When the unit’s condition was compromised, the customer collaborated with RMB to expedite a new lining that matched their planned installation schedule. The metal required repairs, a nondestructive evaluation, and code stamping before being rotolined with ETFE. The entire process was accomplished in three weeks.
Finding quick, long-lasting rotational lining solutions
While a liner failure can pose a setback in operations, rotational lining as a process offers advantages for a quick and long-lasting solution. The first step involves tracing the liner failure to a specific cause, such as using the wrong type of resin for a particular chemical, mechanical impacts, or unexpected thermal cycling. Once this issue is addressed, selecting the proper resin can provide an effective corrosion protection solution.
Rotational lining has a track record of providing excellent chemical resistance and longevity when an experienced staff is in charge and when the resin appropriately matches the service conditions. In addition, rotational lining can provide a swifter and more cost-effective process, especially in emergency situations, compared to other lining methods. The resulting seamless lining can eliminate potential weak points, such as seams or welds, that are present in other lining techniques and might have caused the initial failure.
Facing an emergency equipment failure? Don’t face it alone. Contact RMB for a quick response that can help mitigate financial losses. RMB’s depth of experience assures customers of high-quality services during critical times, to provide a long-lasting and durable solution.
About the Author: Kira Kaleps
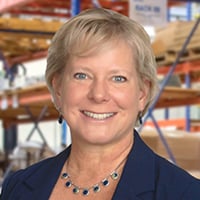